Hydraulic motors have been around for decades, providing rotary motion and power transmission in many industrial applications. Дегенмен, over the years engineers have been pushing the limits of hydraulic motor technology to achieve ever higher rotational speeds. In this article, we will explore some of the key design considerations and technological advancements that have enabled the development of true high-speed hydraulic motors capable of tens of thousands of RPM.
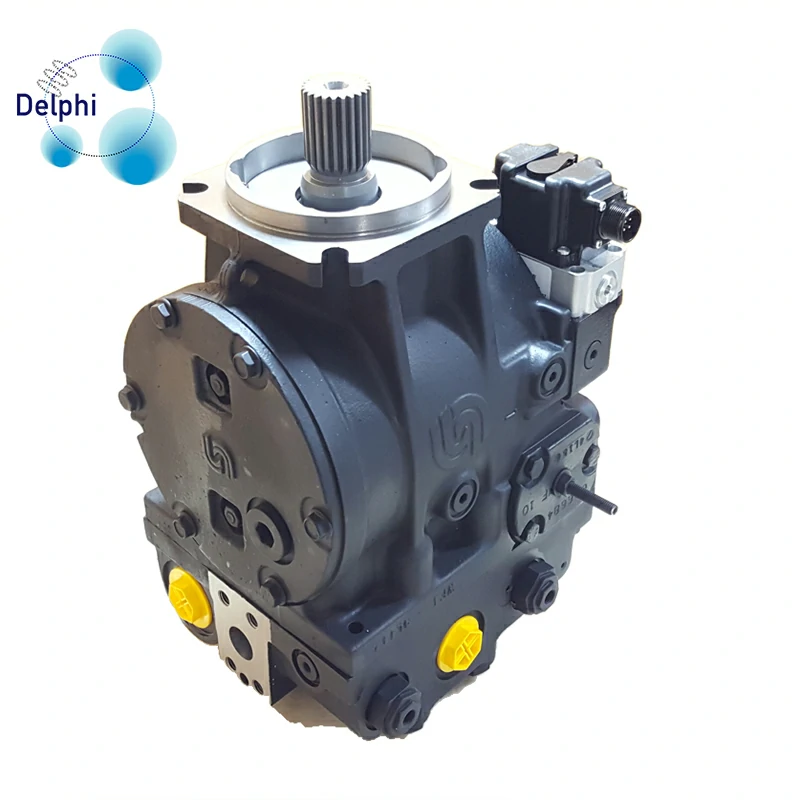
What Does Designer To Consider And Challenge When Designing the High Speed Motors?
Minimizing internal fluid leakage
One of the main challenges in designing a hydraulic motor high speed is minimizing internal fluid leakage. As rotational speeds increase, even small gaps or clearances inside the motor allow increasing amounts of hydraulic fluid to leak from one chamber to another. This leakage robs the motor of pressure and flow, reducing its output torque and top rotational speed. Early hydraulic motor designs relied on static seals like O-rings which do not hold up well at extremely high speeds due to fluid dynamic effects.
Modern high-speed hydraulic motors addressing the leakage problem through innovative sealing technologies. One approach is to use dynamically-balanced face seals instead of static O-rings. Face seals feature two balanced faces, usually ceramic, that ride on a thin film of hydraulic fluid and maintain sealing even at hypersonic speeds. Another sealing solution employs brush seals made of resilient metal fibers. As the motor shaft rotates, the brush seal deforms and conforms to the spinning surface like a brush, maintaining contact and sealing. Both face seals and brush seals greatly reduce leakage compared to static O-ring seals.
In addition to innovative sealing
Hhigh speed hydraulic motor designs minimize internal clearances and flow paths. Shorter flow paths reduce the chances for fluid to leak between stages. Extremely tight clearancing on the order of a few thousandths of a millimeter is achieved through precision machining and assembly. Some motors even use hard-anodized coatings on critical contact surfaces to reduce clearance. These design approaches work together to minimize internal leakage and allow hydraulic motors to achieve speeds in excess of 30,000 RPM.
Fluid filtration is another critical consideration
Fluid filtration is another critical consideration for high-speed hydraulic motors. At higher rotational speeds, even microscopic particles suspended in the hydraulic fluid can cause excessive wear due to increased contact forces. Top motor manufacturers require fluid cleanliness levels of ISO 16/13 or better per the ISO 4406 cleanliness standard. Many also incorporate high-efficiency filtration technology directly into the motor housing, including beta-rated filter elements, magnetic plugs and suction screens. Internal filtration protects against particle incursion and helps components last their expected service life even when operating at the upper limits of speed.
The hydrostatic transmission within high-speed hydraulic motors also undergoes special design adaptations
At tens of thousands of RPM, the dynamic forces acting on transmission components like pistons, swashplates and slider blocks increase enormously. Transmission material selection and part designs are optimized to withstand high alternating stresses from pressure fluctuations and centrifugal forces. Exotic materials like alloy steels, ceramics and carbon fiber composites are utilized where appropriate. Transmission sealing and wear surfaces also employ advanced seals, surface coatings and low-friction materials.
Many hydraulic motor OEMs have extended existing transmission topologies like bent-axis or radial piston units for high-speed use cases. Дегенмен, some have developed novel transmission concepts tailored specifically for hypersonic rotational velocities. One example is a variable displacement “hydrostatic spherical motor” which uses three intersecting spherical pistons instead of flat sliders for increased structural integrity and sealing at extreme operating conditions. Cutting-edge fluid and structural analysis during design helps predict and mitigate potential failure modes.
Thermal management is another critical hurdle for high-performance hydraulic motors
Friction within the transmission and seal interfaces inevitably produces heat, which must be removed to prevent thermal failure and breakdown of hydraulic fluid lubricity. High-speed motor housings integrate efficient cooling schemes such as axial jet impingement, micro-channel heat exchangers, or even integrated liquid cooling circuits. Motor controllers also implement thermal monitoring and power reduction strategies to protect components under excessive temperature conditions.
Conclusion Of New High-speed Hydraulic Motor Applications
New high-speed hydraulic motor applications continue to push technological boundaries. Motors with speeds exceeding 60,000 RPM now enable rotary tools for micro-machining of semiconductors, medical devices and advanced materials. Hydraulic drives for miniature turbochargers and vacuum pumps require 100,000 RPM motors just a few centimeters in size. Extreme-speed direct-drive spindles for aerospace part fabrication are also being developed. Through innovative design, materials and thermal management, hydraulic technology now permits reliable rotary power even at the very limits of high-speed rotary motion. Hydraulic motors are demonstrating they can compete with electric motors in applications demanding ultra-high rotational velocities. As hydraulic science progresses, we can expect to see motors achieving speeds once thought impossible through fluid power alone.