Hydraulic systems use hydraulic pumps to generate high-pressure fluid power that actuates hydraulic cylinders, motors and other components. Hydraulic pumps rated for 3,000 psi and above are needed for applications requiring high pressures and forces. While challenging to design, high-pressure hydraulic pumps enable heavy machinery to perform applications like lifting, braking and forming that would otherwise be impossible. Nel post sul blog, we will discuss hydraulic pumps capable of generating 3,000 psi, their working principles, types and applications.
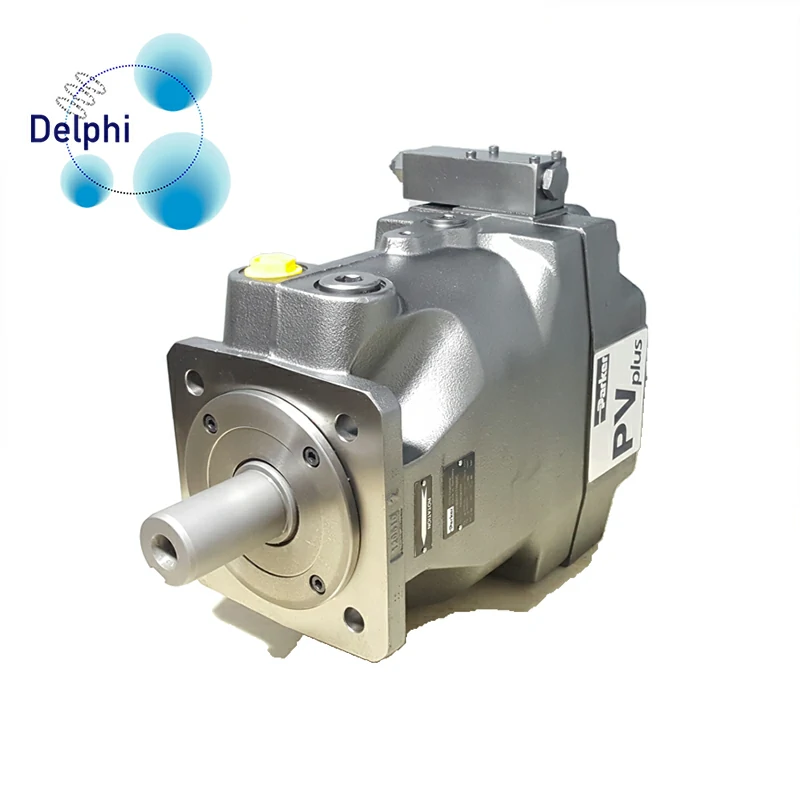
Hydraulic Pumps’ Work Functions And Principle
All hydraulic pumps work on the same basic principle of converting mechanical motion into hydraulic energy. They contain a mechanism that displaces hydraulic fluid and pressurizes it. As the pump mechanism moves, it creates a volume change in one of the pump chambers, which causes a pressure change in the fluid.
There are two main types of pompa idraulica 3000 psi:
- Pompe a ingranaggi: These contain meshing gears that rotate and push fluid through clearance spaces between the teeth. They have a simple design but lower efficiency.
- Pompe a pistone: These contain reciprocating pistons inside cylinders that displace the fluid. Types include axial piston, radial piston and bent axis piston pumps. They are more complex but provide higher pressures and better efficiency.
Both gear and piston pumps can be rated for 3,000 psi and above depending on the pump design and materials used. Common materials used for high pressure pumps include steel, ceramic and various nickel alloys.
Hydraulic Pump Considerations At 3,000 Psi
As pump pressure ratings increase towards 3,000 psi and above, several factors become important in the pump design:
- Clearances: At high pressures, leakage through clearances becomes significant. Very tight clearances and seals are required to minimize leakage.
- Materials: Softer materials like aluminum cannot be used. Hardened steel alloys and ceramics offer better strength and wear resistance at high pressures.
- Lubrificazione: Viscosity and film strength of the hydraulic oil becomes critical at high pressures. Special high-pressure fluids may be needed.
- Pressure ripple: Pressure spikes and ripples increase dramatically at high pressures. This needs to be controlled to prevent damage and noise.
- Cost: High-pressure pumps become more complex and expensive due to the design challenges.
Hydraulic Pump Applications Above 3,000 Psi
Some common applications for hydraulic pumps rated at 3,000 psi and above include:
- Heavy construction equipment: Excavators, loaders, dozers require high pressures in hydraulic circuits to provide high lifting and breaking forces.
- Metal forming presses: Mechanical presses for stamping, forging and extruding metals need pumps exceeding 3,000 psi to generate the high actuating forces.
- Off-highway trucks: Hydraulic systems in large haul trucks and mining vehicles demand high pressures to operate components like brakes, suspension and steering.
- Aircraft systems: Landing gear, flight control and utility actuators in military and commercial aircraft require hydraulic pressures up to 5,000 psi.
- Oilfield equipment: Many downhole tools and hydraulic fracturing pumps operate above 3,000 psi for functions like drilling, well intervention and fracturing.