Pneumatic cylinders are an essential component for automating industrial machinery and processes. One popular option is the Série Rexroth A4VG 32 cylinder from Bosch Rexroth. This post will provide an overview of the key specifications, features and applications of the Rexroth A4VG 32 cylinder.
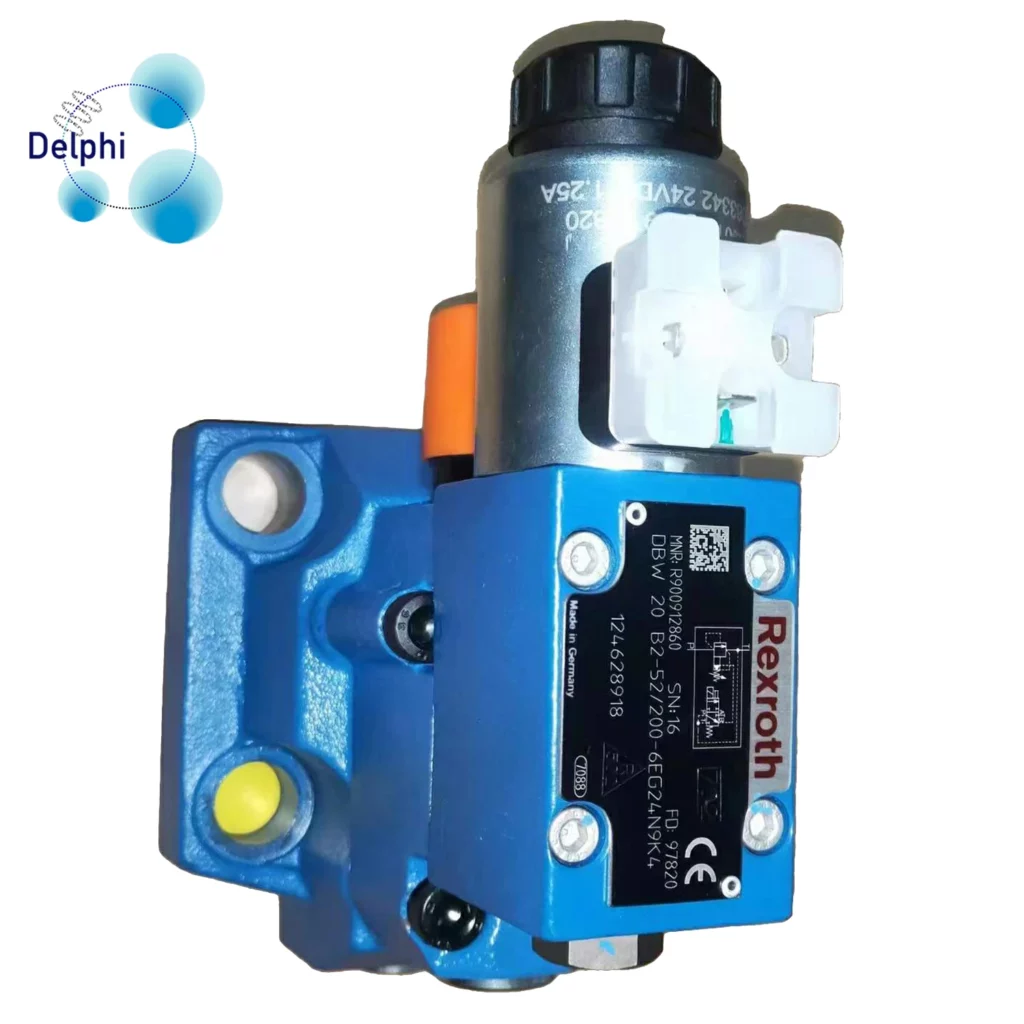
“A4VG” Series Designation
Le “A4VG” in the designation refers to the Bosch Rexroth cylinder series.
- UN – Indicates single-acting (one air port)
- 4 – Stroke length/piston diameter ratio of 4:1
- V – Welded metal rod design
- G – Piston rod style (in this case, round)
Le “32” simply refers to the cylinder bore size in millimeters. The A4VG 32 has a 32mm cylinder bore diameter.
Specifications Of Rexroth A4vg
The A4VG 32 cylinder has these main technical specifications:
- Bore size: 32mm
- Stroke length: 125mm
- Piston area: 804 mm2
- Rod diameter: 16mm
- Maximum pressure: 7 bar (100 psi)
- Maximum force: 6560N
- Cushioning: Available as option
- Port size: G1/4 (BSPP)
Features Of Rexroth A4vg Series 32
The A4VG series cylinders offer several beneficial design features:
- Compact size – The relatively small bore diameter results in a compact cylinder suitable for space-constrained applications.
- High accuracy – The polished chrome bore surface and precise piston rod guidance system provide long-term repeatability under load.
- Low friction – The specially-designed seals and rod guidance reduce friction for minimal air consumption and long service life.
- Sealed construction – O-rings and lip seals protect internal components from debris and contamination, extending service life.
- Durabilité – The welded piston rod and hard-chromed cylinder bore help provide durability over millions of cycles.
- Easy maintenance – The cylinder can be fully disassembled and reassembled for seal and component replacement.
- Options – Accessories include rod holders, different cushioning methods, and double-acting versions.
Applications Of A4vg Series 32
The Rexroth A4VG 32 pneumatic cylinder can be used in several types of industrial applications:
- Clamping andgripping – To securely hold parts for assembly, testing and QA inspection.
- Lifting and lowering – To position, index and transfer parts and materials.
- Force regulation – To apply a precise amount of force for component insertion, joining and testing.
- Punching and stamping – As part of a presses, dies and tooling systems.
- Actuating valves – To open and close valves in pneumatic circuits.
- General automation – Throughout assembly lines and material handling systems.